- Ceramics
- Artist Pages
- Asian Ceramics & Tea
- Ceramics Artist Links
- Ceramics Links
- Ceramics Terms Glossary
- Agateware
- Banding Wheel
- Bat, Throwing Bat
- Bisqueware, Biscuit Ware
- Blistering
- Blow Up
- Boat Anchor
- Calipers
- Carbon Coring, Black Coring
- Carbon Trap
- Chuck, Chum
- Coil
- Colorants
- Crazing
- Downdraft Kiln
- EPK, Edgar Plastic Kaolin
- Electric Kiln
- Extrusion, Extruder
- Fettle, Fettling Knife
- Force Dry
- Greenware
- Kaolinite
- Kilnsitter
- Overglaze
- Pinholing
- Plucking
- Pug Mill
- Pyrometric Cones
- Raku
- Rib
- Sgraffito
- Shelf Of Shame
- Slab Roller
- Slip
- Test Tile
- Knowledge
- Frequently Ignored Answers
- Photography
- Photographers
- Photo Links
- Raw File Converters
- Camera Simulators
- Color Vision Games
- Frequently Ignored Answers
- Resources
- Contact
Force Dry
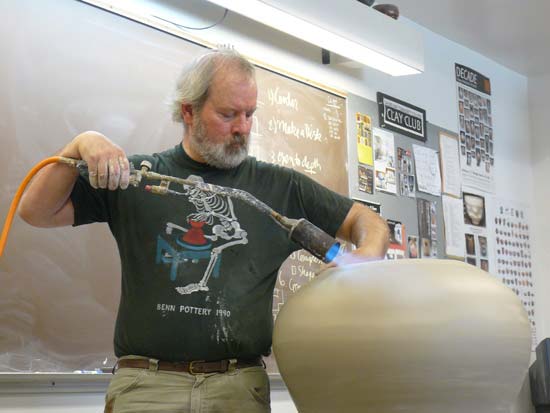
John Benn firming up a pot during a demo at Shoreline Community College.
Using a heat gun, torch or other method to heat and dry soft clay in order to quickly stiffen it to a desired workability. When throwing or coiling pieces, the softness of the clay may not be able to support continued shaping or the addition of more material; a wait period may be necessary to let the work air-dry until it has firmed up, or the potter may attempt to force-dry the piece somewhat in order to continue working. Force-drying clay can cause stresses in the clay that lead to cracking, and should be done sparingly, evenly and with care.
Beginning potters, bursting with enthusiasm (or trying to meet a deadline at the last minute), may think to take a wet, just-thrown piece from the wheel and dry it until it is leather hard and ready to trim. No. No, really - no; it takes more time and energy than it's worth, leaves the clay stressed and too hard on the outside/too soft on the inside, and if the piece is on a (especially plastic) bat, the bat will get burned and warp. If it's your bat, I don't care. If it's mine . . . The best thing to do is find a well-ventilated area and let the piece sit for at least a few hours, flipping it over when the rim is firm enough so that the bottom can dry out.
An example of John's finished work, wood-fired in his kiln. See more here.